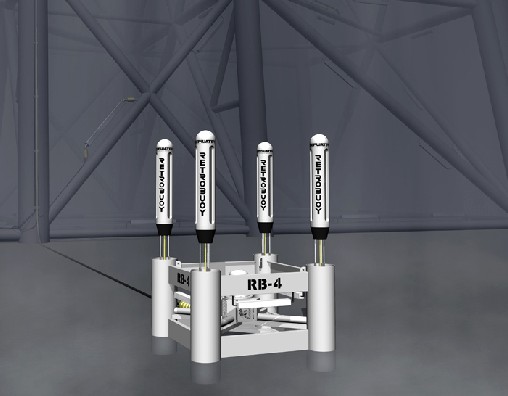
|
RetroBuoy is a remote anode system, ideally sitting approx 100 ft (30 m) from the structure, producing excellent current distribution. |
Product Overview
RetroBuoy is the state-of-the-art impressed current technology for offshore structures. The modular sled based system couples design flexibility with ease of installation using diver or ROV support. With a proven track record of success, the RetroBuoy system redefines impressed current retrofit technology, saving hundreds of thousands of dollars in CP retrofit costs on even modest retrofit programs.
The RetroBuoy system cuts retrofit costs by delivering more cathodic protection, more efficiently with each installed sled. One typical RetroBuoy sled can deliver up to 400 Amps of corrosion protection – enough to protect 80,000 square feet of steel. The conventional alternative protection would need 32 US tons of sacrificial aluminum.
Applications
Offshore platform jacket retrofit.
Very effective on multi-jacket complexes, capable of protecting multiple structures.
Spread-moored FPSOs.
Large dock structures.
Main Benefits
The lowest installed cost in the industry. Installation cost drives offshore CP retrofit budgets: install a single RetroBuoy sled or 48 pairs of sacrificial anodes weighing 500kg each.
Being a remote system, current distribution is optimized, and potential levels are maintained within a tight range over the whole structure.
Exhaustive attention has been given to every design detail; RetroBuoy is modular and redundantly designed.
The design allows the system to be quickly customized to provide sled current capacities from 250-500 Amperes for 15-25 year design life. It also allows us to provide prompt delivery – typically 4-6 weeks from order. |
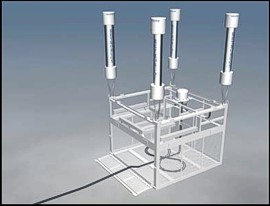
|
|
|
Buoyant anode transport allows system to operate at optimum current levels. |
|
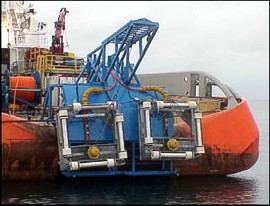
|
|
Two 400 Amp units prior to deployment. |
|
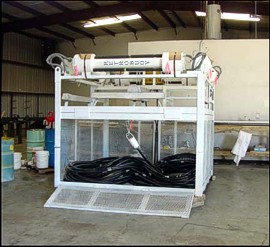
|
|
Available integral cable deployment hopper can simplify installation. |
|
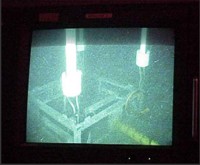
|
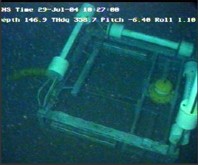
|
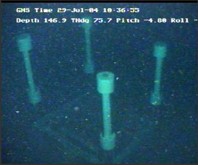
|
RetroBuoy installed on bottom. |
RetroBuoy during float deployment. |
All four anode floats deployed. |
Specifications
Anode Elements: Mixed metal oxide (MMO) activated titanium tubular 1.25” x 48” (31.75 x 1219 mm), center compression connected. Anodes triple coated. Number of rods will vary between 6 and 32 depending on required life and current.
Buoyancy Modules: Tri-part syntactic foam 28 lb/ft3 (0.4485 g/cm3) with depth rating of 1000 f.s.w. (305 meters). Three or four buoyancy modules provided depending on required life and current. Overall dimensions: 12” diameter x 72” long (305 x 1829 mm).
Main Feed Cables: 4/0 A WG (approx. 120 mm2), HMWPE insulated & bedded, contra-helical double galvanized steel wire armor package, HMWPE overall jacket. Two or three cables will be provided depending on required life and current (Note: cable specified is for fixed jacket applications only).
Cable Connections: Made inside an oil-filled, pressure compensated junction box. Each anode element is on a separate parallel circuit.
Tethers: Braided stainless steel.
Frame & Cable Hopper: Welded steel construction, coated and provided with sacrificial anode CP for required life.
Power Supply: Transformer rectifier DC voltage is normally maintained to 24V, but may have to increase to either 36V or 48V for current ratings above 400 Amps or water depth over 250 ft (76 m).